Engineering Control Center
![[shutterstock: 153920459, Brian A Jackson]](https://e3mag.com/wp-content/uploads/2020/12/shutterstock_153920459_cmyk.jpg)
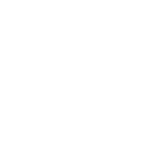
Now the PLM processes are based on a uniform data model and thus also include subsequent logistics control processes across a global production network. With this SAP PLM project, Beumer has laid the foundation for an intelligent customer order structure. This is used to set up customer plants digitally as a backbone and with a uniform database. Beumer can thus optimize its processes from engineering to service and address other strategic PLM issues.
To the benefit of Beumer customers: In July 2020, the first container-based baggage handling system in the USA went into operation in the new Harvey Milk Terminal 1 at San Francisco Airport. As a machine and plant manufacturer in one, Beumer has to break down its internal PLM to individual components as well as describe its complex plant business. Because the projects are becoming increasingly complex and the Beumer Group's business as a whole is also growing strongly, the company decided to switch from its previous in-house developed ERP system landscape to S/4 Hana.
The first step was SAP PLM in the area of engineering. With this solution, Beumer can, on the one hand, represent machine components with many variants and, on the other hand, map its processes in plant engineering and cooperation with third parties. This ensures the mapping of engineering at various Beumer locations in a global structure.
CAD with PLM data model
Beumer took BDF Experts on board for process consulting and also as a project partner.
"In a project of this magnitude, we had to match the new SAP products to our individual requirements." explains Michael Brehe, Head of PLM at the Beumer Group.
"That's why we looked for a partner with the necessary PLM background and proven consulting expertise."
BDF also contributed its Process Control Center (PCC for SAP), an SAP-certified add-on that can be used to efficiently process customer-specific orders digitally. This is done using a fully integrated product structure with multiple views and the automated derivation of bills of materials and orders.
Beumer serves different industries and works for them with partly different CAD systems: AutoCAD, SolidEdge for 3D design, Navisworks and ePlan. The goal of the PLM project was to find a common data model for these CAD systems and the subsequent processes that would flow into SAP. For the integration and management of the CAD documents, Beumer introduced SAP's Engineering Control Center (ECTR). In this context, BDF created a data model for the design data based on SAP's product structure data model.
This SAP solution enables design- and manufacturing-specific information such as product structures (bills of materials), process structures (routings) and factory layouts to be combined in an integrated model. All CAD systems are brought together in an integrated PLM data model. The CAD landscape and the associated processes are no longer isolated solutions, but form a uniform, digital backbone on the basis of which Beumer can use PLM to describe their products holistically from a mechanical, electrical and logistical perspective.
CAD data and parts lists
Michael Brehe: "In our previous PDM system, we held CAD data without extensive connection to ERP processes. With the BDF project, we have laid the foundation for deep ERP integration: from PLM into the downstream processes of logistics and service."
An example of process optimization: Like many companies, Beumer has a global manufacturing system with different production processes. These have different production stages, even for identical products, and thus cannot be meaningfully mapped in the CAD models of the design department. For the logical planning of these production sequences, Beumer uses the BDF software. Contents for the parts lists are defined from corresponding CAD data and additions in the product structures.
Instead of a 1-to-1 relationship between a CAD model and a bill of materials, a 1-to-n relationship is created, which minimizes the effort required for design and increases the benefits for logistics. "We can thus derive as much logistical data as possible in the form of material masters, logistical parts lists and documents from precisely defined order-neutral CAD models," explains Michael Brehe.
As a PLM core object, Beumer has established the so-called eBOM (Engineering Bill-of-Material) as a manifestation of the integrated product structure. Far more than individual material numbers and masters or classic bills of materials, it contains the entire configuration knowledge of a product, its mechanical, electrical and software components.
"You can think of the SAP product structure as a central component of PLM." Michael Brehe describes the functional relationship, "a layer for the holistic mapping of products, on whose data objects PLM processes can then be realized."
Customer asset structure controls SAP
Accordingly, the different variants of the individual components are mapped in the eBOM structure. In reality, each customer plant is highly individual. In large projects such as airport baggage systems, mail distribution centers or cement plants, the individual Beumer machines are assembled, wired and equipped with control units (control cabinets) in specific variant characteristics.
For this purpose, the completely prepared order-neutral product structures representing the Beumer individual machines are digitally transferred into another encapsulated order-specific data model of the product structure (technical order structure). Depending on the customer's plant, a wide variety of production, assembly or installation bills of materials for the individual order are thus created from the generic eBOM.
At Beumer, this technical order structure is called the "customer plant structure". All further processes in the SAP system are controlled via this structure: the procurement of purchased parts, the production of in-house production parts, the triggering and coordination of subcontracting and sub-supplier processes, product and project costing at all necessary levels of detail, and integration into project management, i.e. triggering of individual requirements depending on the central project deadline control depending on the individual work packages, and assignment to the correct account assignment objects.
SAP for the PLM processes at Beumer went live at the end of June 2020. This laid the foundation for the PLM area, on which the logistical follow-up processes can be built from 2021. The Corona crisis hampered communication at the start of the project; as a result, training for the 800 users at 14 engineering locations worldwide could only take place online. Nevertheless, the project remained on schedule.
In the future, the new procedure will enable the machine and plant manufacturer to have engineering departments across the entire group of companies work globally with a uniform data structure - a digital backbone - and no longer with individual systems, as was previously the case. To complete the PLM, the Beumer project team led by Michael Brehe also focused on the period after commissioning, i.e. the actual part of the life cycle of the customer's plant. Therefore, a complete generation of the service object structures was set up using SAP Service Management.
All maintenance-relevant objects or individual parts of a plant are managed via so-called equipment structures. Here it is possible to plan, monitor and document maintenance intervals, repairs, machine running times and the replacement of wear parts. This data can be used, among other things, to establish early warning functions, perform statistical evaluations and optimally manage the operation of a plant as a whole.

Beumer Group
The Beumer Group is a leading international manufacturer of intralogistics systems in the fields of conveying, loading, palletizing, packaging, sorting and distribution. With 4500 employees, Beumer generates annual sales of approximately 950 million euros. The family-owned company was founded in 1935, is owner-managed and independent in the third generation.