Digital retrofit as the basis for successful store floor integration
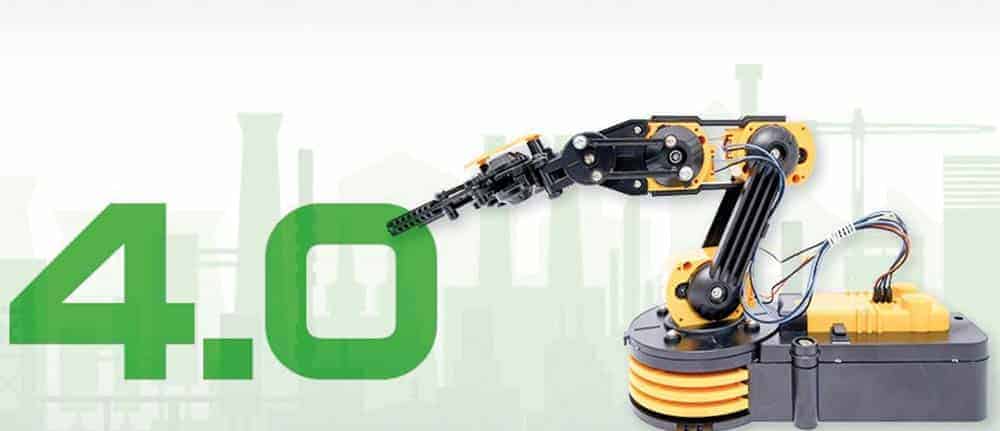
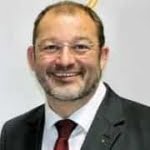
The company's targets are clear. Flexible and transparent production, automated determination of key OEE figures, condition-based maintenance processes such as predictive maintenance, real-time reporting of key production and quality figures, and real-time feedback of current production order data into higher-level systems (e.g., SAP) enable the company to react quickly and flexibly to changes and to hold its own against competitors in the market. So much for the theory.
Such Industry 4.0 solutions are made possible by comprehensive plant integration, in which process values and data can be read directly from machine controls or IoT devices via existing interfaces.
But what does it look like in practice? A quite common picture of a medium-sized company is characterized by a heterogeneous machine landscape.
Machines from a wide variety of manufacturers and of different ages are found together in the production halls. The average service life of machinery at the 40,000 or so companies in Germany's manufacturing sector is around 20 years.
And a large proportion of these machines are not Industry 4.0-capable. While modern machines usually already have functions and sensors for recording relevant machine signals, this is not usually the case with old or existing machines.
Added to this is the different lifespan of hardware and software components in the plants. For example, mechanical systems are often designed for a long service life of many years, while IT and software solutions quickly become obsolete and can usually have several updates during a plant's service life.
According to a study by KfW, SMEs in particular are often reluctant to engage in digitization due to concerns about having to purchase expensive modern machinery and the associated high investment costs.
It doesn't always have to be a new acquisition. By means of a digital retrofit, existing plants can be retrofitted with new sensors and communication technology in a cost-effective and task-oriented manner and thus made fit for Industry 4.0 applications. A complete retrofit of production plants is not absolutely necessary.
Depending on the task, it is enough to know which aspects of the production process need to be digitally monitored and controlled. The next step is to network the objects concerned. This is usually done by using so-called IoT gateways.
With the help of IoT gateways and corresponding framework technologies, data from a wide range of systems and manufacturers can be combined and connected to higher-level IT systems.
The data can be read out from controllers, such as Siemens, Beckhoff, Rockwell or WAGO, via OPC-UA, Modbus or one of the other common interfaces such as CANopen or RS232.
Already at field level, a large amount of the recorded data can be filtered and cached so that the complete data can be accessed at any time, but data transmission is not burdened by unnecessarily high data transfer.
Combined with information from higher-level IT systems, such as SAP ERP, SAP MES, external PLM or other third-party systems, it is quite easy to compile information for controlling production, automate feedback information, realize real-time visualization of production and quality information on the store floor, and thus create real added value for the company.
So, Mr. Meier (or whatever your name is), your task is clear. Start at the grass roots!