Not an end in itself
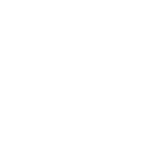
Quite a few companies are struggling with the quality of their master data. Since poor data quality can, among other things, impair business processes, lead to incorrect decisions and make it difficult to comply with laws and guidelines, companies are regularly advised to set up professional master data management.
Of course, this costs money and therefore raises the question of return on investment. The success of master data management in relation to the capital invested is not so easy to answer in "hard" figures, but there are empirical values from projects and assessments by those involved in the process that allow statements to be made about the return on investment.
Let's first take a look at the typical problems that companies have to deal with. Creating customer and supplier master data is usually a lengthy process, and media discontinuities in the processes are the rule rather than the exception.
A high error rate in data creation and maintenance results in frequent changes, especially in address data and bank details. A duplicate check often does not take place. Since an overview of "supplier groups" and "customer groups" is regularly missing, the negotiating position in purchasing and sales is weakened. Poor data quality leads to incorrect deliveries and returned mail (mailings, invoices, etc.).
In the case of material master data, the mere fact that a material master data record in SAP MM (Material Master) can have up to 1000 individual fields means a special challenge. Of course, not always 1000 fields are occupied, but 150 to 200 may well be (depending on the company and material different).
In addition to the global master data that applies to everyone in the same way, there is plant-dependent data that increases the amount of data. In addition, many departments are involved in the master data process for material (purchasing, sales, scheduling, etc.). This means that there are very many process participants and communication and coordination take up a lot of time - without a master data system and without data governance.
Many companies also allow hundreds of "occasional users" to create material master data; for them, the creation and maintenance are extensive and confusing. Therefore, professional master data management focuses on reducing the number of users - and thus also the number of potential sources of error. With master data management, the attempt is made to authorize in a more targeted manner and thus to permit who creates, enriches, changes and releases master data in the first place.
A closer look at the costs of poor data quality and the consequences of long lead times when creating master data makes it clear where the "set screws" are and what potential master data management holds.
Costs of poor data quality
Experience shows that hardly any companies are able to prove the costs of poor data quality with hard facts, i.e. with figures. What they do know, however, is that incorrect customer and supplier master data incurs costs for incorrect deliveries and orders, postage and labor costs for mailing returns, and a great deal of work for cleaning up and correcting errors.
In addition, they often have no overview of the order volume from the same supplier, which results in excessively high prices in purchasing. Inadequate material master data generates costs, for example, due to invoice items that are too low because of incorrect parts lists and excessive logistics costs because of incorrect weights. Increased complaints due to faulty deliveries, incorrect material orders and production downtimes due to missing materials are further cost drivers.
Long lead times when creating customer and supplier master data lead to delayed orders, and when creating material master data lead to a delayed go to market. If a company does not know when a material is "ready" in the system to start production, it ends up delaying go to market. Regardless of the master data domain, long process lead times result in delayed shipments if a product cannot be ordered in a timely manner.
Employee dissatisfaction is compounded when they do not know when "their" material is ready for them to continue working, or when they have to constantly correct errors; employee productivity drops. Finally, customer dissatisfaction threatens when no reliable statement can be made about when what will be delivered if it is not known where the business process currently stands.
Basically, master data management creates added value on two levels: on the one hand in the administrative areas, for example through more efficient master data maintenance processes or also in IT projects; on the other hand through increased transparency in the operational areas and thus improved control capability - turning data into insights into value.
The benefits in the context of master data maintenance processes and IT projects can be seen, among other things, in the reduced effort required for data searches, lower internal reconciliation effort, and the absence of duplicate work for data changes or initial entries. Furthermore, clean master data forms the basis for scalable automation options and reduces the effort required for migrations, for example during S/4 Hana conversions.
The benefits of MDM in administrative and operational areas as well as for compliance ultimately increase the competitiveness of companies. Good data quality also ensures the satisfaction of customers, suppliers and employees.
Return on investment
If you want to express the benefits of master data management in figures, you have to rely on empirical values. In the case of customer and supplier master data as well as material master data, the main factors influencing ROI include the number of master data installations and updates, the duration of throughput times and manual coordination efforts, and the follow-up costs in the event of incorrect data and duplicates. For material master data, the number of production sites with plant-specific material master views is added.
Those involved in master data management projects estimate that an MDM tool can reduce processing or turnaround times by up to 50 percent. A significantly lower coordination effort contributes to this.
A faster go to market is difficult to state exactly, but the following example gives an idea of the potential: If a company reports that it takes 70 days for a new material to be fully created in the system, and you extrapolate that to the number of parts that are built into a product, then you get an idea of what can be achieved with a system that reduces the material creation time from 70 to a few days (e.g., two to three days in a specific case).
Another empirical value states that the error costs resulting from process intransparency can be reduced by 80 to 90 percent. The reason: master data management ensures complete transparency along the entire process chain, so that it is always known where the master data process stands. According to estimates, 53 percent of the data can be found more quickly and easily. On the question of the ROI of master data management, KPMG provides the following supplementary figures on specific business metrics:
Three to eight percent reduction in process cycle time: reduced data search effort, reduced data reconciliation effort, no duplication of data entry efforts, reduced reconciliation needs, process automation opportunities.
Two to five percent reduction in spend: efficient pooling of purchasing volumes, better negotiating position for purchases, creditor structure and pedigrees that can be analyzed; improved commodity group management to know what is sourced from whom; information to evaluate suppliers; faster onboarding of suppliers when the process for master data is in place.
Four to seven percent lower IT project costs: less data migration effort because there are fewer problems with M and A activities or system harmonizations because data first comes into the ERP via the master data system; less data cleansing effort; less system complexity because a master data system transfers the master data; and decreasing maintenance effort.
One to two percent improved sales growth: better negotiating position, transparent, uniform pricing conditions, evaluable customer master data and pedigrees, improved identification of cross-selling potential.
Five to ten percent reduction in working capital: efficient inventory management and lower inventory costs when, for example, it is known that ten materials that have only a slight discrepancy in master data are actually one material, and consequently the required inventory only needs to be held for one material (less double stocking); improved invoice verification, efficient revenue and receivables management.
In addition to these quantitative benefits of master data management, KPMG also names some qualitative advantages. These include reduced risks due to fewer data protection breaches, fewer customs and tax risks (compliance), and reduced credit risks. Even with analytics, master data management not only offers advantages, but is essential.
For example, if you offer predictive maintenance, you have to have your master data under control so that you can find the object that requires maintenance. KPMG sees further advantages in leveraging automation potential if you know what you can derive from the master data, and in an improved reputation through smooth deliveries, fewer complaints and a correct customer approach.
Conclusion
Master data management is not an end in itself, but rather has an indirect and direct influence on the value of the company and can become a competitive differentiating factor. This applies in particular to new or modified business models, such as the enrichment of traditional business models with service-focused business areas.
