Increase energy efficiency, reduce production costs
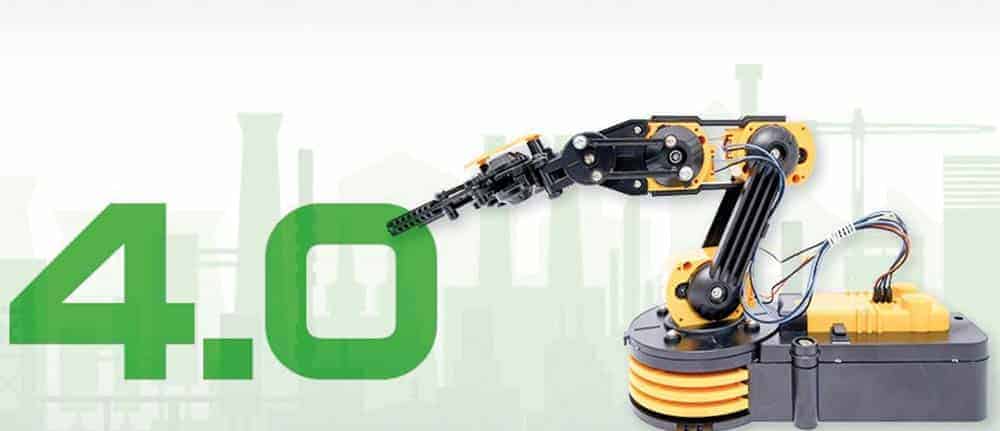
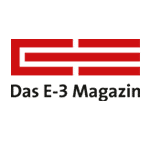
The progressive networking of company processes, keyword Industry 4.0, is also generating more and more energy data as a result, opening up new avenues for energy-efficient and economical planning.
The companies G.I.B, IFM and QOSIT are currently developing a system solution that uses sensors to measure precise energy consumption data and then feeds this directly into the ERP system. Although many manufacturing companies have long relied on energy-saving machines and heating and cooling optimization, there is still a lack of suitable systems for recording and analysing energy consumption data in many places.
Until now, many companies have only used direct measurements in the production process via sensors in order to obtain indications of potentially necessary maintenance work based on deviations.
This is good, but it is by no means sufficient for efficient planning and process management. Professional energy data management creates comprehensive transparency and enables the company to optimize production processes based on the information provided by the ERP system.
Increasing energy efficiency
The use of smart data promises an economical solution here. Together with IFM, a global provider of sensors, controllers and systems for industrial automation, and QOSIT, a specialist in the centralization of business-critical data, the software manufacturer G.I.B is currently developing a system solution for energy data management that enables optimal control of energy efficiency:
The exact energy consumption data is measured by sensor and fed directly into the ERP system. In this way, large energy consumers could break down their energy consumption costs precisely to the manufacturing process, right down to the unit production.
This would mean a significant reduction in overheads, as the precise allocation of costs according to source would ensure sound economic planning and unprecedented cost transparency at unit, machine or plant level.
The solution can also set a new course in terms of emissions. Precise knowledge of the energy supply enables highly reliable statements to be made about the emissions generated in the production process.
Decisions on whether, when and where a batch is manufactured can then be made dependent on whether the CO2 emissions generated during production are compatible with compliance guidelines or the desired life cycle assessment.
"Although our system solution is not yet ready for the market, the test setup already shows how innovative and sustainable the system solution will be"
says Björn Dunkel, member of the G.I.B management board.
The demonstration shows a Carrera track whose energy data is measured by a sensor and displayed on a monitor. The information obtained flows into the connected ERP system, where it triggers specific recommendations for action or, if necessary, error messages.
They are also available for analysis and planning. Transferred to the production process, each lap could represent a manufactured part. In this case, the measured energy consumption per lap = energy consumption for the production of one piece.
This information could also be combined with "Time per round" = "Time per piece production" and "Heat development per round" = "Emission per piece".
All the data together then show the production/round speed at which emissions and energy consumption are within the desired corridor.
The minimum and maximum speed per track section, which is measured by when the car flies out of the curve or falls out of the loop, would also provide information in a figurative sense about the production speed at which quality defects and rejects are to be expected.
Conclusion:
An economically profitable approach that is guaranteed to provide a lot of pleasure in the future, and not just in the model.