Mass customization thanks to digital twins
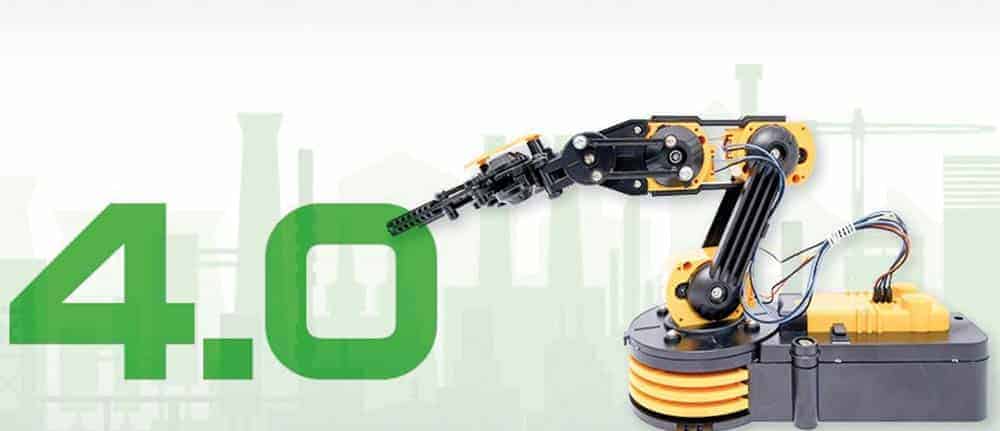
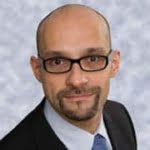
Mass customization is the symbiosis between highly personalized products on the one hand - and the quality and production advantages of series production on the other.
The smaller the batch sizes and the more complex the tasks, the more indispensable powerful automation becomes. The "time to market" and "time to customer" time lines, i.e. the span between the individual order and delivery, cross at the manufacturing level in actual production.
ERP, e-commerce and modern configurators have already significantly accelerated order management processes. Online trade and the retail market clearly show how an optimized supply chain can disruptively change an entire market segment.
Since real processes have not yet been accelerated as quickly and elegantly as digital commerce, progress in design and real manufacturing is still lagging considerably behind. In other words: extraordinary potential lies dormant here!
The design of new components traditionally focuses on function and design. Rarely are considerations of producibility consistently thought through from the outset. This is where the worst time killers lurk.
How often is the store floor left alone with existential questions, such as how to insert the assembly into the machine or how to reasonably reach the drill holes with an angle drill head? Resulting feedback and feedback loops cost time and resources.
For mass customization, the process must consist of flexible and iterative control loops. It won't work without an intelligent division of the individual process steps and a continuous data feedback across all manufacturing levels.
Efficient data management, so that each process receives exactly the data it needs, is essential. If you want to shorten "time to market", this is where you start. Digital twins of plants, with SAP integration and connection to CAD systems, have proven to be a viable concept.
A new product is designed, simulated and initially produced virtually with all details. The program code for the robots and machines is generated digitally from the CAD data, loaded onto the virtual controllers and validated there (software-in-the-loop).
The true-to-life mapping accurately reflects problems and changes - only much faster and without interrupting ongoing production. Every change and every new variant is first tested virtually on the digital twin.
Then the real plant is coupled to the digital twin (hardware-in-the-loop) and the new programs are loaded directly onto the machines and robots in the process chain.
The trend towards ever more individualized products is leading to increasing product variants with simultaneously decreasing quantities. The use of robot-based applications will therefore increase continuously and cover in particular small batch sizes up to one-off production.
In end-to-end digital production, it no longer matters whether material is printed, separated, joined or transported during a process. Just as it no longer makes any difference whether this process step is carried out by a machine or a robot.
In additive manufacturing, i.e. industrial 3D printing, various digital twins can provide valuable services. Bionic design and so-called lattice structures enable a completely new product design. The result is components that are extremely lightweight and highly resilient.
Hybrid manufacturing, in the context of metallic 3D printing, means the integrative combination of additive and subtractive manufacturing processes. The printed parts are then mechanically processed and refined, for example by milling, tapping or polishing.
As a rule, very heterogeneous data and system technology is integrated. The hybrid approach is a sensible complement to the advantages of both methods, while at the same time compensating for the respective disadvantages.