Model maintenance back in the field
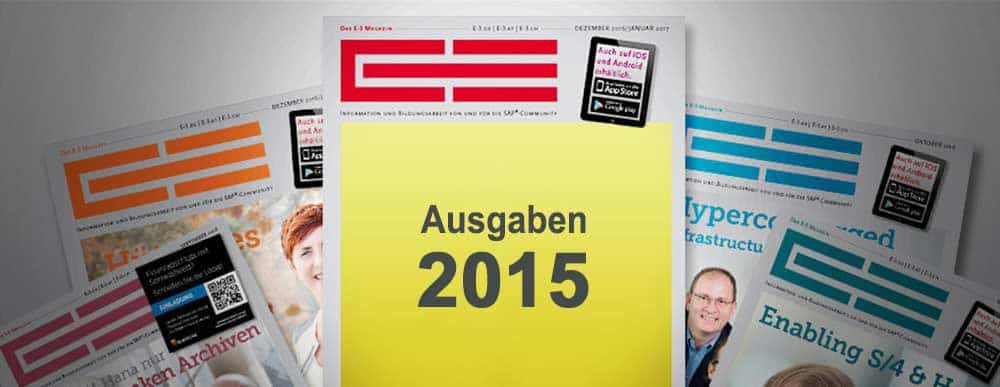

Chemical accidents that contaminate the environment and drinking water and thus endanger people's health or even their lives unfortunately happen again and again.
One of the most serious accidents of this kind occurred in 1986, when toxic firefighting water leaked into the Rhine near Basel, causing mass fish kills.
It was precisely in this year that Helmut Dennig founded Denios in Bad Oeynhausen, Westphalia. The company focuses on developing and producing storage solutions in which hazardous materials can be stored safely, reliably and in compliance with the law.
Today, the company has six manufacturing sites and 17 branches in the most important markets in Europe in the USA and China; in 2014, around 700 employees generated sales of just under 141 million euros. The specialist for the storage of hazardous substances faces global competition.
In order to be able to manage growth in a targeted manner in the future, it is important for the company to have powerful IT processes, from sales to purchasing and production planning, right through to financial accounting and controlling, and to design and harmonize them across all locations. Denios relies here on the integrated functions of SAP ERP.
"The use of SAP software is an important component of our business and IT strategy"
says Michael Kallenberg, Head of Information Technology.
The processes defined at headquarters are - as far as possible - established as standard in the subsidiaries.
Variant diversity under control
"For each individual product, there is a wide range of variants and thus configuration options to choose from"
Kallenberg explains.
The efficiency of the processes involved in product configuration and quotation generation is therefore a factor relevant to competition. For this purpose, Denios uses the Treorbis Variant application, an Abap-based add-on that is seamlessly and release-securely integrated into SAP ERP and linked to the SAP standard objects that are relevant for product configuration, such as bills of materials, routings or condition determination.
In this way, Sales can carry out configuration processes as part of quotation creation quickly, securely, transparently and in high quality directly in the SAP software.
"In the container sector alone, there are on average 150 different variants for each product, which differ, for example, in terms of size, doors - sliding, wing or roller doors - interior fittings or air conditioning and ventilation systems"
clarifies Michael Kallenberg.
A pharmaceutical company that needs to safely store laboratory samples has different requirements for a security room than a company that needs a fully equipped server room for data backup.
Especially for this purpose, for example, the experts at Denios have developed the Complete Data Center (CDC), an innovative IT container system that protects the IT infrastructure from failures as well as from a K-fall caused by fire or vandalism.
With the variant solution from Treorbis, the employees in the design department can now conveniently enter their know-how about the configuration and combination options of the individual products in tabular form and make it available to the sales department.
Special know-how, such as that required to build up and maintain SAP relationship knowledge, is not needed for this, so that model maintenance is now fully anchored in the specialist area again.
The time-consuming coordination with the internal IT department is eliminated and the process is significantly streamlined.
"The time savings achieved so far have already paid for the expenditure on the Treorbis solution"
Kallenberg is pleased.
Many things have also been simplified for end users in sales: Today, they can see immediately in the SAP system whether the desired model variant is technically feasible and can calculate the price and delivery date.
The bill of materials and routing are generated automatically and, once the order has been approved, forwarded directly to the work preparation department in production, which immediately triggers the next steps.
As a result, the entire order processing process not only runs much more reliably, but also significantly faster. This improves delivery reliability and increases customer satisfaction.
Space for core tasks
Sales staff are relieved of manual activities. Item-specific bills of material and routings can now be derived directly from maximum bills of material and routings, which are provided with a set of rules that are evaluated during the configuration of a customer order.
This leaves the sales department more room for core tasks such as order processing and consulting, which requires particular care, especially for safety-relevant products.
This is possible because in the variant solution the entire set of rules for a product is stored centrally in "decision tables". This means not only a simplification of data management, but also higher data quality.
Until now, every single routing had to be created by hand and checked again. Until recently, around 70,000 routings were laboriously stored and managed in the SAP system in this way.
With the introduction of Treorbis Variant, Denios has also optimized the form-based processes. The sales department can create individual offer forms and supplement the product and configuration data with individual texts as well as integrate photos, graphics or drawings.
This is ensured by an interactive print control based on the SAP solution extension Interactive Forms by Adobe, which automatically posts the additional entries in ERP.
During the implementation of the add-on, those responsible relied on the process and consulting expertise of Treorbis in the area of variant configuration.
Even during a test installation, it became clear that the variant solution met the company's specific configuration and quotation requirements particularly well.
Thanks to the tight implementation schedule and the proven methods of the SAP full-service provider, the implementation was completed quickly.
"A significant contribution to the rapid commissioning was made by the goal- and result-oriented cooperation of all persons involved in the project as well as the high personal commitment of the Treorbis consultants, who were available at all times and implemented change requests promptly"
praises Kallenberg.
Currently, two of the five product lines in the Container Division are mapped in the new variant solution. The remaining three lines are to be integrated by the end of 2015.
Since the learning curve also rises steadily in the course of a project, the mapping of the second product group was completed almost twice as quickly as the first.
The approximately 60 end users enjoy working with the variant solution because it is easy to learn how to use. At the same time, they have the option of editing table entries on the familiar Excel interface and uploading them back to the SAP software using an upload program from Treorbis.
Mobile 3-D configuration
Kallenberg draws a positive conclusion:
"Treorbis Variant creates the basis for fully SAP-integrated, transparent and efficient variant configuration in high quality."
The next steps, such as the rollout of the variant solution in all companies and an improvement in the display of data structures in the configuration editor, are already in the pipeline.
In addition, the company wants to make the order processing processes in the field sales department more efficient with a mobile scenario. This will involve product configuration at the customer's premises using a 3D model on a mobile device.
Once an order has been placed, the data is transferred directly to SAP order entry.
"With an appealing 3-D display, we can even better meet the expectations of customers who nowadays want the same convenient configuration experience in the store as in the home in terms of haptics and ease of use"
Kallenberg concludes.