Industry 4.0 enabler
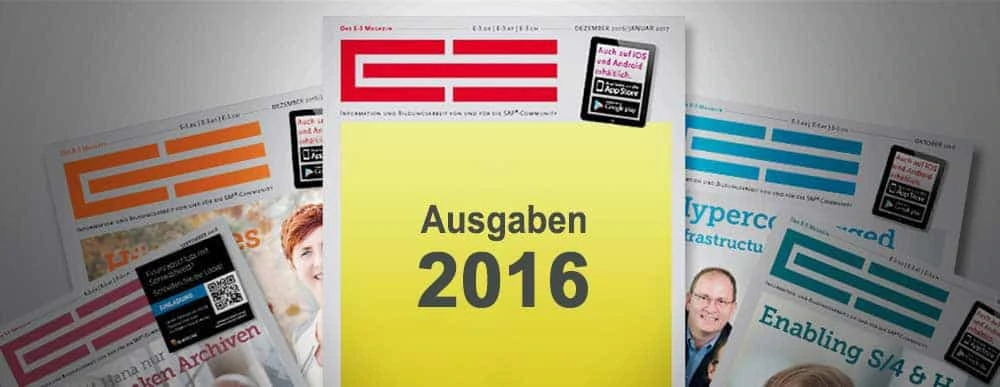
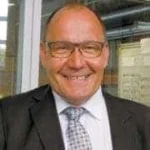
The digital transformation is heralding a paradigm shift to a new form of industrial production - Industry 4.0. German industrial companies expect this to boost productivity by an average of 3.5 percent per year over the next five years, according to a study by PwC subsidiary Strategy&.
A "fully automated, self-controlling factory", the Smart Factory, creates the basis for innovations and completely new, disruptive service and business models.
Just think of batch size 1 production, i.e. of exactly one product according to customer requirements at costs equal to series production, predictive maintenance or consumption-oriented on-demand payment models for plants and equipment.
Intelligent networking of technologies
The technology for this is available. Today, automation solutions, control, scale and print systems exchange data with machines or other IT applications via interfaces and the Internet. Auto-ID components, such as barcodes and RFID, are also largely mature, as are sensors and actuators.
The trick is to intelligently link the individual technologies with the commercial and logistical processes of the ERP system - through both horizontal and bidirectional vertical "real-time integration".
In this way, an Industrie 4.0-compliant value network with end-to-end digital data flow is created. At the same time, the volume of both structured and unstructured data is swelling exponentially.
This flood of data (big data) can be evaluated on the basis of predefined algorithms and intelligent follow-up processes can be triggered in "real time". ERP systems such as SAP ERP are suitable as the heart of a smart factory.
To optimally support Big Data analyses, SAP ERP can additionally work with powerful in-memory technology, such as the Hana platform based on this technology.
Integrate processes bidirectionally
For companies whose IT strategy is based on SAP ERP, a smart technology platform that is one hundred percent integrated with SAP is suitable as an Industrie 4.0 enabler: The MPS platform creates the basis for a completely automated factory.
MPS helps to dialog, network and visualize data and processes in production and intralogistics transparently and in "real time". Another advantage is that devices, sensors and subsystems are connected directly to SAP ERP without additional middleware and the data from the systems of different manufacturers can be processed in a standardized manner with the same logic.
Process data from machines, industrial controllers, scales, PCs on the production lines, OPC servers as well as Auto-ID components are available to the processes in the SAP ERP system in "real time".
The result is a fully integrated process chain whose individual elements interact with each other and provide a "real-time view" of what is actually happening in the factory, which is then used, among other things, to align the operational planning and control processes.
Complete tasks easily and quickly
The requirements for user-friendliness, always a demand of the various user groups and specialists in production, from shop-floor workers to managers, must also be taken into account.
If SAP transactions and data as well as processes and information from the store floor are visualized clearly and in "real time" on an intuitive, industry-standard interface, users can complete tasks even faster and more efficiently than before, whether on the desktop or mobile via smartphone, tablet or notebook.
Changes to the layout of the user interface can be made by the user with little effort - if the user is authorized to do so. The technologies of the Multi-Process Suite are, on the one hand, the enabler for SAP-based Industry 4.0 processes and, on the other hand, the development basis for a modular Manufacturing Execution System (MES) that is integrated seamlessly and release-safe into SAP ERP.
Interaction ERP and MES
Orbis MES links and synchronizes processes and data from the store floor with ERP processes. A web-based, intuitive interface clearly visualizes the data and key figures from manufacturing in "real time".
They can be called up at any time on any end device at the touch of a button. This makes value creation in production truly transparent, and problems such as excessive scrap, excessively long setup times, and incorrect or missing operating resources are identified immediately.
In this way, measures such as rescheduling a production order to another machine can be initiated immediately and expensive downtimes can be avoided.
Track every movement in real time
As an enabler, MPS efficiently supports SAP-based intralogistics by integrating barcodes and RFID. In this way, processes can be tracked and controlled seamlessly in "real time" from goods receipt to warehousing and internal transport to picking and shipping processing.
Likewise, on the basis of this current information, automated control loops are used to ensure the inventory security of the warehouses through appropriate replenishment strategies.
If components and semi-finished products are equipped with a barcode or RFID, every movement between the processing steps can be recorded in a mobile and dialog-supported manner and tracked and visualized in the SAP system virtually in "real time".
Each part can be clearly identified and located at any time. For example, digital tool management can be implemented to clearly identify the location of each individual tool and optimize tool inventory - with a positive effect on costs.
The data collected in the course of digital mold management can also be used for predictive mold maintenance as well as for optimizing processes in production.
RFID and barcode technologies also enable the traceability of products along their entire life cycle. Information about the origin, storage and condition of products can thus be retrieved at any time. This complete documentation helps, for example, to narrow down sources of error in the event of complaints.
These examples show:
- Intelligent linking and "real-time integration" of processes along the value chain pave the way to the smart factory
- This path can be taken in small steps in the form of pilot projects
Industry 4.0 step by step
Many companies, especially in the SME sector, lack an Industry 4.0 roadmap. Many are still reluctant to invest here because they lack an overarching 4.0 strategy. According to a McKinsey study, 40 percent of companies are inadequately prepared for Industry 4.0 in terms of strategy and expertise.
However, this should not lead to not approaching the topic of Industrie 4.0 without a roadmap. For these companies, a strategy of small steps in the form of sub-projects is recommended, through which they can introduce elements of Industrie 4.0 in their factories.
The investments required for this are manageable, as the existing infrastructure is used and no new hardware needs to be purchased. Existing SAP systems and processes are improved by connecting them to machines and people and automating them - from the individual machine to the production line to the entire factory. This makes it easier for medium-sized companies in particular to enter the smart factory.
When planning and realizing Industry 4.0 projects, an experienced partner can help by competently supporting companies in making existing technologies and solutions such as SAP ERP part of the Industry 4.0 processes through integration.
The starting point for each project is a workshop. Experts record the requirements in order to develop a concrete concept for the further procedure on the way to the smart factory.