Mastering the challenges of the future
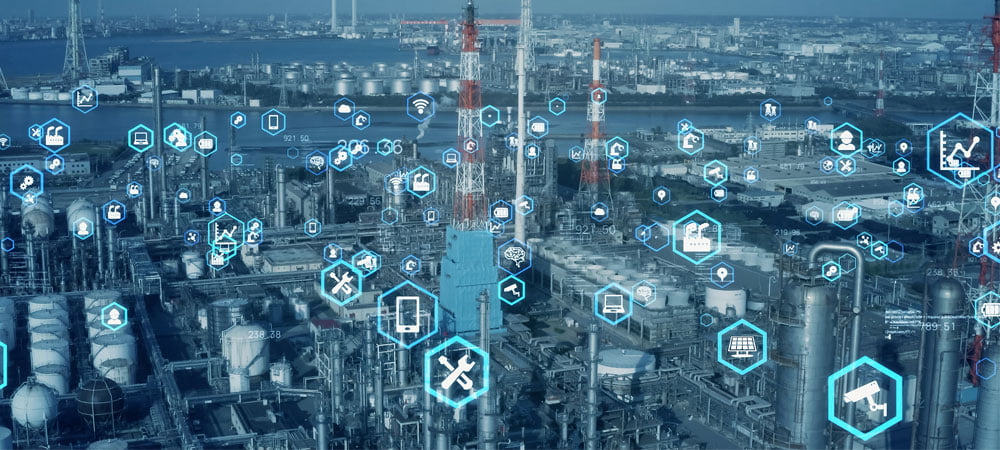
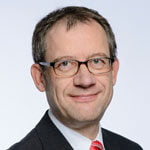
Logistics 4.0
BLG Logistics, headquartered in Bremen, is a seaport and logistics service provider with an extensive international network. The company looks back on a 145-year history and is globally active with almost 100 locations and branches in Europe, America, Africa and Asia. In the three business units Automobiles, Containers and Contract, BLG offers its customers a wide range of logistics services. These include, for example, automobile transport, production and fashion logistics as well as special projects, such as the handling of fragile aircraft parts or factory equipment weighing several tons.
To better respond to current and future challenges, the BLG Automobile division decided to digitize its planning processes. The tool of choice was SAP Integrated Business Planning - IBP for short. This is a SaaS solution that creates transparency about requirements, inventories and capacities along the supply chain. Innovative forecasting methods and planning algorithms for sales planning, production, distribution and procurement support targeted inventory optimization and thus ensure delivery readiness across the entire value network. Simulations of various planning scenarios also help users to maintain an overview of the consequences of changes and decision alternatives as part of what-if analyses.
The Bremen-based company chose the SAP specialists from Consilio in Munich as its implementation partner. The consulting firm is not only an SAP Gold Partner, but has also been awarded the Recognized Expertise Supply Chain Planning and Logistics as well as S/4 Hana and Financial Management certificates by SAP several times.
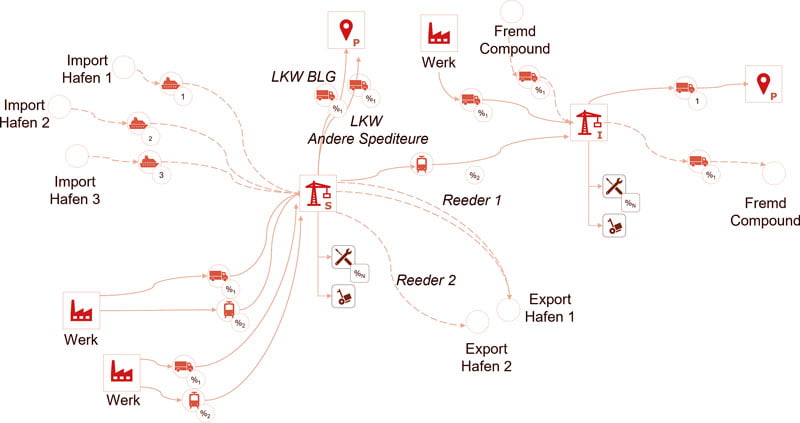
Strengthen competitiveness
The current economic and political upheavals are putting pressure on logistics service providers in particular. Examples include the accident in the Suez Canal in 2021 or the current container congestion in the North Sea. The loss of proven transport routes by road and rail due to possible extreme weather conditions or sanctions must also be planned for. To enable companies to proactively take countermeasures, they need end-to-end digitally networked solutions that provide them with maximum transparency and information in real time. Although this will not prevent the disruptions, it may reduce the negative impact on day-to-day business. BLG Automobile wants to achieve this goal by mapping demand and capacity management (BKM) with SAP IBP, enabling it to strategically plan the entire terminal and transport network. The Bremen-based company hopes to generate more synergies as a result - not only economically, but also ecologically. To achieve this, it is necessary to store the entire network on road, rail and water in IBP - as a digital twin - in order to increase integration and transparency. On this basis, the data from the internal BKM can then be compared in IBP to identify capacity quantities, surpluses or shortages - the keyword here is congestion management.
This is intended not only to minimize deviations, but also to develop new solution concepts and scenarios for and with the customers in the long term from the knowledge gained, which can be evaluated on a fact-based basis. An additional module was added to the BKM to evaluate the scenarios. It serves to quantify both cost and revenue accounting as well as ecology (CO2 balancing) and to bring them together in a uniform system with volume and capacity planning.
This is how the system looks
The digital twin of BLG Automobile's complex network and flows of goods are mapped in SAP IBP as follows: It consists of four location types, plant, compound, port and dealer, with a total of more than 700 nodes that are connected to the eleven BLG automotive terminals via transports (arrows) with four mode types (more than 30 carriers/shippers/shipowners). The terminals are not only infrastructure, storage and buffer for the car manufacturers, but also hold capacities for a technical preparation of the products (value-added services). Around 1700 products as an abstraction of vehicle models from all manufacturers are transported via this overall network, with a special version for each product being mapped as part of the overall network, for example for the 1 Series BMW or the Mercedes C Class. In other words, each product has its own network of specific characteristics within the overall network. In IBP, these versions can be represented flexibly at different levels with the desired level of detail.
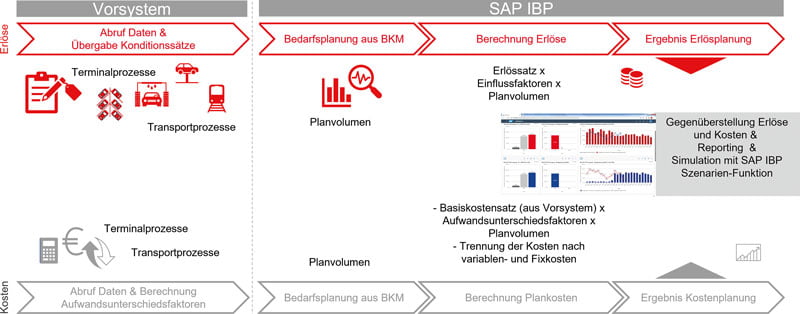
Special planning logic
Unlike in the supply chain of a manufacturing company, BLG's car terminals are both the warehouse and the buffer for car manufacturers. Therefore, there is no classic push-and-pull logic here. This means: On the input side, the cars are delivered according to a push principle that is based on the manufacturers' production schedules. The outbound side, on the other hand, operates according to a pull principle, as the focus here is on the sales plan of the vehicle dealers.
The problem for BLG was therefore to bring these two different principles together in an innovative way, since there is no universal causality between inputs and outputs. The solution was to use two approaches by which inputs and outputs are planned separately and then compared. As a result, two independent forecasts are produced, reflecting the difference between inputs and outputs. By comparison: Manufacturing companies typically plan their network end-to-end.
At BLG, the basic process is divided into three basic steps: Transport to terminal, terminal handling, onward transport. As a result of the requirements planning for the inbound and outbound processes, the requirements for the sub-processes can be derived. If BLG is the carrier, this can be realized for the terminal and transport process. In parallel, capacity is modeled and planned for each of these steps. To do this, BLG's experts use IBP's time series analysis and incorporate customer forecasts, internal expert estimates, data from market data providers and shipping companies - this then forms the forecast.
The comparison of demand with capacity shows very clearly where action is needed. Capacity surpluses or deficiencies can thus be easily identified. This gives planners the opportunity to identify potential problems at an early stage and allows timely proactive countermeasures. The best demand and capacity planning does not help a company if it lacks an overview of costs. For this reason, BLG has developed individual cost and revenue planning that can be used to determine the costs for each process.
The Bremen-based logistics service provider benefits from this in two ways. First, it receives a clear fact-based picture of how the cost and revenue situation is looking, and second, this tool can be used to simulate what happens when a process changes. Typical questions here are: What is the effect on the revenue and cost side of a change in route or mode of transport - for example, from truck to rail or ship - due to disruptions or rising costs?
The analysis is based on capacity planning and the underlying processes. To obtain a realistic assessment, BLG first identified all sub-processes and then mapped them digitally. The terminal processes include movement processes such as inbound and outbound according to the respective modes of transport (ship, rail, truck, own axis), technology and storage. In addition to the terminal processes, transports by truck, rail and inland waterway vessel are integrated into the costing model. Revenue and cost information about the processes is recorded in the upstream system and then transferred to IBP. The revenue and cost planning is created from the various planned volumes via the costing model. In the process, the costs are divided according to contribution margin levels. This makes it possible to create a wide range of analyses in terms of economic impact. For example, conversions from truck transports to rail transports can be evaluated directly with the economic impact. In addition to the big picture, however, it is also possible to drill down at any time in order to analyze the cost and revenue situation in detail and thus, for example, to show the profitability of the technical groups.
Sustainability in view
The basis for CO2 balancing is again formed by the requirements and capacities from demand and capacity management. In order to make the emissions tangible, BLG's Sustainability Department defines factors according to the Greenhouse Gas (GHG) Protocol - Scope 1 to 3, with which the emissions can be calculated. Here, parameters such as terminal processes, buildings and terminals, lighting, technology and storage as well as transport processes are included in the assessment. For example, emission factors per vehicle or hour are determined. Which factor is used depends directly on the process. A technical process is assessed per hour, as workers or machines are active here on a time-dependent basis, while the incoming and outgoing loads are assessed per vehicle. BLG records emission factors at different levels and then calculates them - one level is the energy sources fuel oil, gasoline, electricity or gas, while another includes the consumption of energy for buildings, lighting, transports within the terminal and so on. In IBP, Scope 1, 2, 3 and X emissions can be calculated in this way, along with volume planning, to document the company's sustainability.
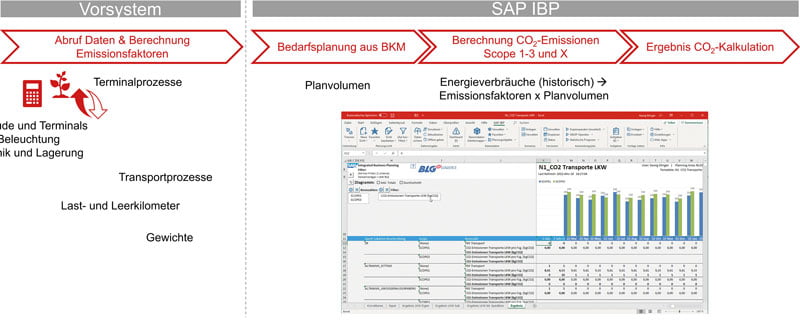
IBP in practice
Managing a supply network as complex as BLG Automobile's requires innovative strategies. That's why BLG worked with Consilio to come up with a strategy for implementation. The requirements were up-to-date, transparent planning and a permanent exchange of information between the stakeholders involved in the company. The tools of choice were therefore SAP IBP for Sales & Operations and the collaboration tool SAP Jam. But how does the interaction work? First, the entire network is considered. IBP then analyzes the network and uses its algorithms to create a forecast of all nodes and all requirements within the network. In order to obtain a realistic picture of all demands and capacities, a link was also created to manual forecasts, for example via BLG sales staff or customer forecasts. In the course of this, the planning data of BLG's customers - i.e., car manufacturers, dealers, shipping companies, and rental and leasing companies - are fully integrated. The subsequent overall observation and analysis of the network, which also includes an analysis of the alerts, helps to identify the first problems within the network. These include bottlenecks in the network or over- and under-utilization, for example if transport areas or load carriers are not being used to capacity. The sales department benefits particularly from this, as it is given the opportunity to intervene in a controlling manner.
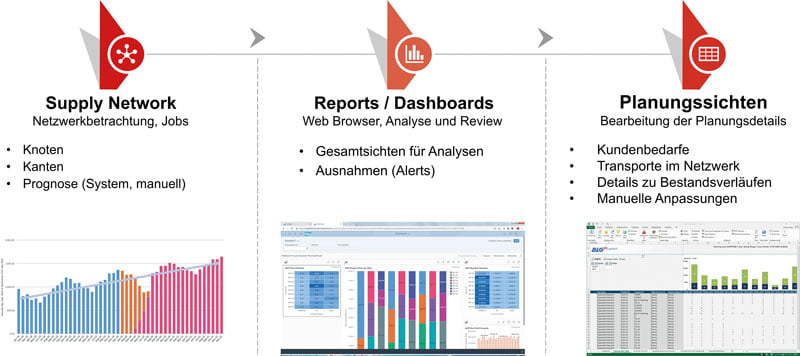
Do not break over the knee
Numerous detailed planning views help to increase user-friendliness and enable employees to carry out planning in the complete network according to requirements. In doing so, they always have an overview of customer requirements and transports - alert views and details on inventory progress are also permanently available. In addition, it is possible to make manual adjustments at all levels of the network at any time. To better reflect the specifics of intercontinental sea transports, BLG developed a specially adapted planning logic, which Consilio also implemented as a highly individualized component of the system. All these adjusting screws are mapped in the network planning and can be individually adapted there. Implementing IBP in a complex environment is no small feat.
It is advisable to carry out the project in several steps so as not to overload the company's own IT and to involve the people in the company. BLG and Consilio therefore divided the project into three stages. In the first part, the concept was created in about four to five months and over 1000 customer-specific key figures were recorded - including truck bases, port facilities or terminals. One example: In IBP, the number, berths, berthing times, frequencies and loading capacities of ships are stored and the utilization of the quay infrastructure and modes of transport are displayed with these. The implementation phase took about one year until go-live. The module of cost and revenue accounting and CO2 balancing was implemented in the second part, which also took about one year. During the implementation of the project, it became apparent that the stages gave the company and its employees the time they needed to absorb and internalize all the changes.
Always informed through Jam
At BLG, there is a very large network in which you have to manage the monthly planning process and also control short-term adjustments or exceptions. For this purpose, Consilio has mapped extensive workflows together with BLG. They are carried out monthly by default, but can also be triggered ad hoc if required. They include demand planning, capacity planning and balancing, congestion management, cost and revenue planning, CO2 balancing, and scenario planning. To promote collaboration between the different departments, BLG relies on the SAP Jam solution. The collaboration tool enables a much faster exchange of information and know-how within the company and also with customers. Consilio has linked the two solutions. The workflows were mapped in Jam in great detail. Administration takes place centrally.
In the first step, BLG Automobile has digitized medium and long-term planning in strategic terms with IBP. In the long term, the concept is to be transferred to operational planning. It is also planned to further improve the system through optimization. The focus here is primarily on CO2 balancing and economic efficiency. Furthermore, additional data sources are to be connected to the system.
SAP Jam: Always informed
With the collaboration tool SAP Jam, problems and tasks in the company can be solved together. Employees are more connected and customers, suppliers and external partners can also be integrated into the system. The intuitive cloud software is available on the move at all times and brings useful social functions into the everyday work of businesses. It reduces complexity and creates the basis for a more team-oriented work culture.
With SAP Jam, employees can share documents and ideas about issues or projects instead of doing so via e-mail or other communication channels that are more difficult to manage or track. The following functions are available:
Enterprise Social Networking: Company administrators invite users to join various groups where they can share information, documents and files on specific topics, hold discussions and clarify issues.
External Collaboration: SAP Jam can be used as a cross-enterprise collaboration platform, for example, to engage in dialog with customers or suppliers, provide information, and provide first- and second-level support.
Structured Collaboration: Brainstorm together, solve problems or make decisions: In a chat-like environment and with the help of pro and con tables, rankings and voting tools, the members of a group can find their opinions more easily. These functions are also being used more and more frequently in idea and improvement management.
SAP S&OP: What if ...?
AP IBP for Sales & Operations (SAP IBP S&OP) provides integrated processes for synchronizing sales planning with supply and financial planning. In addition, other areas such as research and development, procurement or external stakeholders can also be integrated. SAP IBP S&OP enables a constant exchange through weekly or monthly review meetings. This enables coordination and decisions for the entire supply chain to be made on a uniform data basis (single source of truth). Integrated Excel planning views and Fiori dashboards also ensure uniform and intuitive user guidance and enable optimal use of relevant functions such as simple statistical demand planning, infinite supply planning or opportunity and risk planning. If required, functions from other IBP modules can also be integrated or simulations performed, for example on order quantities or shift operations.
DSAG Annual Congress: Experience BLG Logistics live
Bremen-based logistics service provider BLG Logistics has digitized its strategic planning processes in the automotive logistics business unit with SAP IBP and is also benefiting in the long term. If you want to delve deeper into the topic, come to the DSAG Annual Congress in Leipzig. On October 11, 2022 at 3:00 p.m., Marcus Bolte, Head of Business Development and Network Management at BLG Automobile, and Georg Klinger, Partner and Senior Solution Architect SCM at Consilio, will talk about how they were able to meet the Bremen-based logistics service provider's demanding requirements with SAP IBP. The speakers will be available - as far as possible - for interested visitors to exchange ideas. Additional information is available at booth B3.
