Electronic Shelf Labels
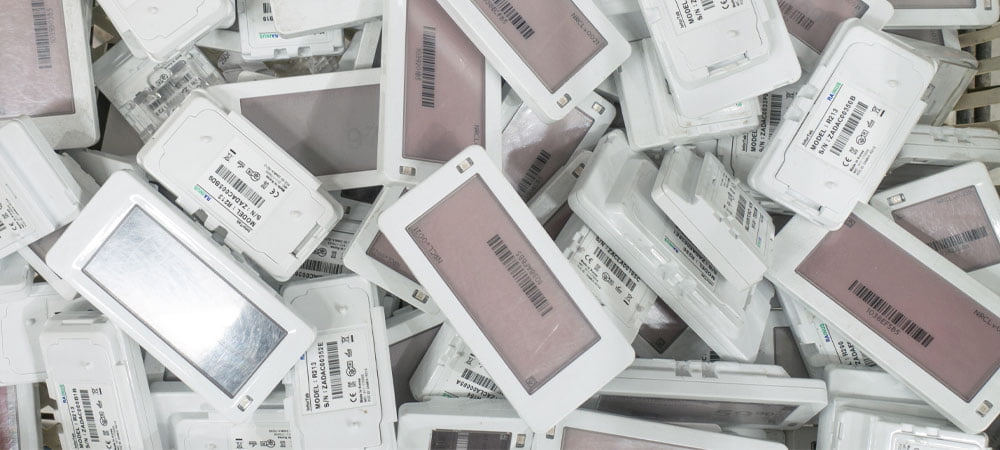
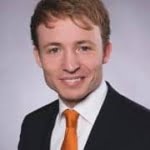
Use cases for trading with V-Cloud, Captana and SAP systems
Electronic shelf labels can be used in a variety of ways. Wholesalers and retailers are among the companies that are particularly far advanced in the digital transformation. With current technology trends and developments such as omnichannel services, in which stores, central warehouses, online stores and social media are connected in real time, retailers want to offer their customers an attractive and seamless shopping experience across all channels.
The changes are also visible on the shelves. In many stores, the old paper price labels have been replaced by modern electronic shelf labels (ESL). The reason: paper labels require a great deal of manual effort. With each update, new labels have to be printed and attached to the shelf by employees. This costs time, ties up capacity and can lead to errors. For example, prices on the sign and at the checkout often do not match quickly enough; sometimes new awards are even lost altogether. Customer complaints and additional work for the staff at the checkout are the result. If such problems occur more often, in the worst case it can have an impact on the retailer's reputation.
Electronic shelf labels, on the other hand, help to make work easier or free up space for more important tasks, such as sales talks, the provision of goods or services. This in turn contributes to customer satisfaction. The savings in the price labeling process and the free capacities also result in the cost-effectiveness of electronic shelf services. In addition, use cases such as pick-by-light and Nosbos (not on shelf but on stock) make it worthwhile. Digital displays are also more environmentally friendly: the software behind them consumes hardly any power, requires little maintenance and has a long service life.
Electronic shelf labels can fulfill various functions. These include, of course, electronically depicting the classic functions of a shelf label. This means that they also display the product name and price, as well as other information as required. In addition, they are linked to the retailer's ERP system. This enables central control of the labels without employees having to approach each label separately. In addition, the information on the shelf labels can be compared in real time with the data in the ERP system, such as SAP S/4.
This function can be expanded to include integrated NFC chips. The chips enable communication with smartphones, for example. Customers can then call up additional information or - if rows of shelves are empty - pre-order products in the web store.
The LED lights integrated in electronic shelf labels offer potential and can be integrated into certain business processes such as pick-by-light and put-by-light. This can be used to support employees, for example by color-coding products or pre-orders from the online area in the retail store. Different colors can indicate different customers (orders). If you take this concept a step further, you can even use the LEDs to show walking routes so that employees can pack pre-orders in an ideal way.
Not on Shelf but on Stock
Digital solutions are considered essential to remain successful in retail in the future. The ERP system is becoming the central adjusting screw for retail. With a modern ERP as a basis, many digital solutions can be integrated to optimize retail processes. With Navi Nosbos, there is a proven software in the area of Electronic Shelf Labels that runs in parallel to the Vusion Retail IoT Cloud platform and mainly connects the solutions V-Cloud, Captana and SAP systems. The software combines the most advanced ESL technology, IoT low-power communication infrastructures, high-resolution color displays, sensors, active NFC, ultra-fast data transmission, LED lighting systems and computer vision. This is how brick-and-mortar retail becomes a digital asset.
The software is often integrated into the existing SAP ERP system, so that no isolated applications are created. Navi can be implemented per location within a few weeks and during ongoing operations. In this process, all labels are replaced with electronic displays and provided with live data as well as information on current prices and promotions. The electronic shelf labels are addressed via radio using a special access point.
The introduction is followed by a test phase. During this time, empirical values are collected on suitability for everyday use, speed, time savings and reliability. Experience has shown that companies start further conversion processes on the basis of this data. Electronic price labeling is often used as a standard feature in remodeling and new construction of existing locations and is then also the gateway to further digitization of the sales floor. It is conceivable, for example, to integrate an employee mode: By switching the label to a second level, this shows important internal information about the item, such as current stock, MRP indicator, order stock and sales figures.
