Machine Learning: Opportunities for Mechanical Engineering
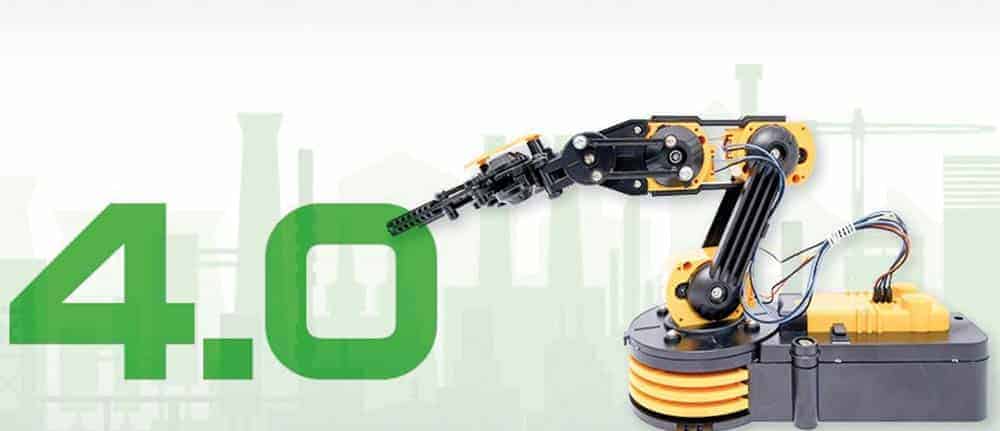
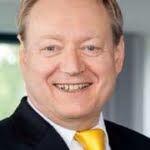
The demands on the production of the future are high, because the markets are becoming increasingly volatile, the number of globally active market participants is growing and products must be customer-specific.
At the same time, expectations of production quality are high. This requires more flexible, responsive production systems and employees.
Industry 4.0 has become an absolute trend topic in the manufacturing industry as a result of these developments. Industrial companies that want to be successful have to deal with the topic and the smart factory.
In Industry 4.0, all components involved in the production process as well as people are networked with each other. Communication and thus information are important production factors.
Industry 4.0 is not possible without software. Technologies that enable Industrie 4.0 include cyber-physical systems, but also the use of mobile devices in production.
New possibilities
The result is agile and collaborative production in network structures that better meets requirements than previous production concepts.
Industry 4.0 enables many new business models. In mechanical engineering, the individual machine becomes a commodity and thus interchangeable. It is the software in combination with sensors and controls that makes it unique.
Therefore, in the future, it will no longer be about the spare parts business, but about availability and value propositions.
In logistics, the focus will be on services, such as the use of drones as feeders.
Predictive Maintenance
For the tasks of predictive maintenance, the benefits of Industrie 4.0 become particularly clear: In production, sensors and embedded systems can detect the wear of critical components of a machine and proactively transmit it to a software platform.
This analyzes the real-time data and optimizes the maintenance plan for the team of service technicians. This makes maintenance truly plannable and will dramatically change the service business.
However, many medium-sized machine manufacturers have neither sufficient IT nor business analytics expertise. This must be made available. After all, what is the point of collecting a lot of data without being able to interpret it and make it useful?
In order for machine builders to remain competitive in times of digitalization, filtered machine data - not process data - must be recorded decentrally, collected centrally and evaluated. These evaluations are valuable both for the machine builders themselves and for customers of the machine building companies.
Data analysis as a subscription
This is where providers of manufacturing execution systems can help. After all, MDE and BDE are important components of MES solutions.
The operating and machine data collected with the help of an MES can form the basis for important business analyses. This enables new business models.
This service is conceivable as a rental model (time and/or data volume-dependent, cancellable on a three-monthly basis) or as a business analysis that can be booked on a monthly or weekly basis.
This has the decisive advantage that there are no major investment hurdles for potential customers. The path toward Big Data and Industry 4.0 is thus also made possible for smaller companies.
Conclusion:
The extraction and evaluation of the data results in numerous advantages - for machine builders and their customers! Thus, machine builders can constantly monitor their machines and plants via dashboard and a high availability is guaranteed.
In the area of predictive maintenance, the optimum maintenance time can be predicted and scheduled. The customers of the machine builders can be guaranteed a high degree of reliability and thus absolutely reliable planning.
In this way, machine builders and their customers can jointly achieve higher machine performance and availability, and service concepts can be optimized.